Truing up is the term for squaring the warp and weft of a fabric, so that the weaving is truely squared. While it is not necessary for some projects, I am a die hard truer upper!
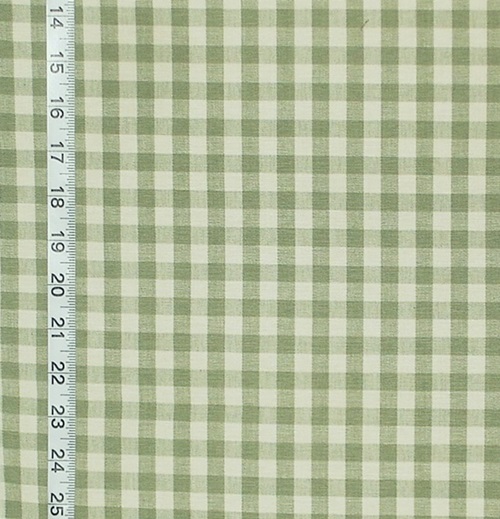
WARP and WEFT
The warp threads run up the roll, one warps a loom. The threads that go back and forth, from side to side, are the weft threads, also called the fill, as they fill the warp threads. They also form the selvedge edges. They turn over the edge warp thread to start another line of weaving. The warp threads create the grain, the weft threads stabilize them.
In checked fabrics, one can easily see the warp and weft threads.
And, one can also see if they are out of true!
Warp threads go up the roll.
Weft threads go across the fabric.
The point of truing up is to get the warp and weft threads to run perpendicular to each other. When a fabric has been trued up, one can use it, knowing the material is being used on what is called on grain. Why is it important? When a fabric has been trued up the finished item has a better chance of remaining in the shape one intended for it- curtains will hang straight, napkins will remain square.
How does fabric get out of true? Perhaps when it was woven, the weaving was not quite correctly done. Perhaps the tension on either the warp or weft weaving lines was not even. Or it might not have been stored properly. Depending on how the material has been stored the fabric can warp out of shape. If fabric is stored rumpled, over time, the fibers will retain that shape, which warps the fabric.
Does all fabric need to be trued up? No. If one wants to make a small wine bag, it is not necessary. But, say one wants to make napkins with mitered corners. One would want to true up, so they don’t turn into parallelograms. Want your curtains to hang straight? True up!!
TRUING UP FABRIC
So, how does one true up fabric? The goal is a fabric with the threads running straight in both directions, up the warp, and across the weft, at 90 degrees to each other.
People think that fabrics with what look like a diagonal weave can’t be trued. But, a diagonal weave is just a visual effect. The warp threads have been woven across the fabric, not at an angle. For instance, a denim, which is a twill, looks as if it has a diagonal weave. But, the threads have just been woven in and out of the warp, over two threads, under one, and the weaving pattern is staggered, creating the diagonal effect. The threads go straight across the fabric. Most fabrics can be trued. Some are just harder to get there.
STEP ONE- Creating Straight Edges
The first step is to remove the selvedges. They are often tighter than the rest of the weaving, and can be puckered. So, one is going to remove them, following a warp thread up the fabric. Moving in from the selvedge, find the place you want to be the new fabric edge. Snip from the bottom edge upward across a few of the weft threads. Remember, the weft goes across the fabric. This allows one to snag a few of the warp threads to the side of the snip. One is going to use those threads to create a path along which one can cut to remove the selvedge.
I always start by gently pulling on a couple of the warp threads, gathering it up the length of the fabric. If the piece is long, I will at some point break those threads, and pull them out, and cut along the path that has been made by their removal, and then find the broken ends and fish them out with a pin and continue up the length of the material.
If the threads are very fine, I gather them, and don’t cut as I gather. If the colors of the pattern are dark on a light background, as I gather, the colors printed on the thread shift out of their place in the pattern, which gives me a visual guide along which to cut. If the threads break, I pull them out, with the help of a pair of tweezers and a safety pin, cut to the place they broke, and continue up the fabric.
Then, I do the other side of the fabric. And, I do the same thing on the top and bottom of the material. When all sides have been done the all edges of the fabric follow a single line of warp or weaving.
STEP TWO- Checking for True
Now it is time to check how true the fabric is. The goal is to end up with the corners being 90 degree angles, with the new edges lined up. So, fold it in half, lining up the sides that had been the selvedge edges. When matched up, are the top and bottom corners at 90 degree angles? If so, the fabric has been trued up. If not, it is time to work the fabric back into shape as best one can.
STEP THREE- Manipulating the Fabric
Unfold the fabric. Starting at the bottom right corner, use one hand to grasp the right hand selvedge edge near the corner, and the other hand grasp the bottom edge, near the same corner. And, pull your hands away from each other, in a diagonal direction. Move your hands along each edge, pulling the fabric, on the bias, in a diagonal direction. When your hands get to the corners, continue along the adjacent edges, still pulling the fabric on the bias.
When done, go to the opposite bottom corner. And put your right hand on the bottom, and the left hand on the left selvedge edge and pull in a diagonal motion, on the bias, and continue along the edges. You are now pulling the fabric on a diagonal in the opposite direction from before.
One often reads about just taking the opposite corners and jerking on the fabric, and then doing the same at the other corners. But, that does not move the threads evenly. The threads in the middle of the top, bottom, and sides, are not being repositioned evenly, if at all.
Check the fabric again. Fold it in half, matching up the old selvedge edges, match up the corners, and check to see if the corners are 90 degree angles. When one is done one should have a fabric that has the warp and weft threads running true, or as true as one can get.
Another way is to fold the fabric in half, matching the selvedge edges, and pin or clamp it across the top, and down the selvedge edges, and then start manipulating the fabric realigning the threads.
TRUING UP TO A PATTERN
So, there can be a few issues about truing up. The most common has to do with pattern placement. In a perfect world of fabric printing, the pattern would always be printed straight onto the fabric, with the grain. Well, that is not always the case! As fabric is printed, fabric is moving very quickly. And, the pattern can be printed crookedly on the fabric. So, say one is doing curtains, using a fabric with a strong pattern which has not been printed straight on the grain. What is one to do?
One does not want curtains with a pattern running up or down across the curtains! One has to manipulate the fabric to get the pattern to line up the way one wants it. One has to true up to the pattern.
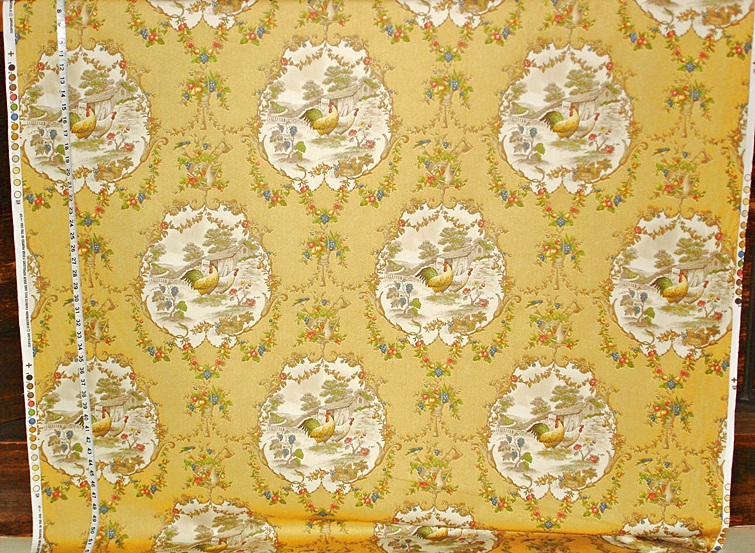
Let’s use the chicken fabric as an example. Say the chicken pattern was crooked. One would not want the medallions to be going up or down across the curtains. One would have to true up to the pattern.
The first steps are to true up the fabric. The selvedges are removed as usual. And, one trues the fabric.
Then one needs to get the pattern placement correct for the project. One curtain maker I know has a 5′ long piece of aluminum. It is about 2″ wide, and flat. She got it at the local hardware store. She lays out the fabric, places the metal bar on the fabric, above the pattern, and clamps the bar to the table. Then, she starts moving the fabric up and down, under the bar, to get the line she wants. She says she likes it as she can step back, and really look at how the pattern will look on the finished curtain, and decide what is best.
When she gets the top line that she wants, she marks it, makes 90 degree angles at the top corners, and measures down the fabric, continuing to check the pattern layout.
When she finished she has a fabric that is trued to the pattern, but is off grain.
She feels, and I know it is true, that people see the pattern, not how the threads lie. And, as curtains are hung, the weight of the fabric pulls the fabric down evenly from the rod or from whatever it is hung from, keeping it straight, even though the material is not trued up, just the pattern.
A lot of people don’t want to bother to true up. And, if one is working with a lot of fabric, it can be time consuming. I actually like it. Doing it gives me a sense of how a fabric will be to work with. And, if one wants the project to come out the best that it can, one needs to do it. I will say it again… TRUE UP!
_______________________________